A High-Performance Central Warehouse
The Bründl Sports Group has worked with Xvise to implement a sports project: The regional warehouse in Kaprun was converted into an efficient central warehouse in record time. Perfect conditions for a top-quality service and further growth.
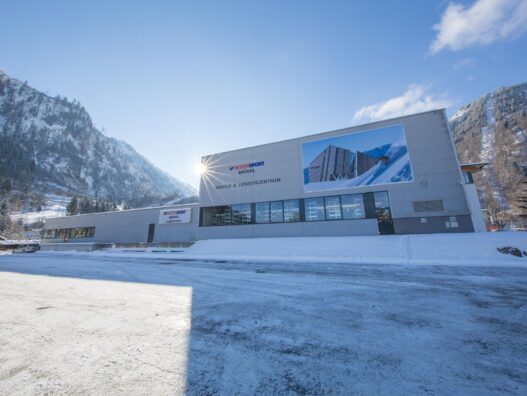
"With Xvise we developed new central logistics as a project with a challenging time-scale and were very impressed by the outside-the-box approach of the Consulting team.
The excellent cooperation was guided by structured, goal-oriented workshops, fast development work and perfect implementation monitoring.
Thereby, applying the best requirements for all processes which target operational excellence."
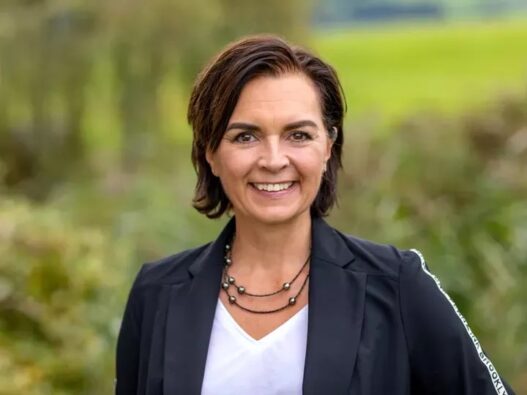
Logistics in top form
In the 1950s, even before the Kaprun skiing area was made accessible, Hans Bründl started a success story in the region, offering crafted sleds and skis. Today, the Salzburg family business operates 23 stores at seven locations, employing a staff of more than 365. Obviously, growth still is a significant item on the agenda of the sporting goods retailer. Against this background, Bründl decided to transform the existing regional warehouse at the Kaprun headquarters into a high-capacity central warehouse for all locations with the support of Xvise. In the course of this project, an appropriate delivery concept was going to be worked out for the retail outlets as well.
From regional to central warehouse
For this purpose, our logistics consultants collected all relevant data, analyzed processes and recorded the existing physical structure and organizational circumstances. The next step was to prepare a concept for the central warehouse. Our experts needed to determine space requirements, suitable storage technology and equipment and to design the future warehouse processes. This included all steps from receipt of goods, labeling and security via storage and picking through to packaging and distribution to the retail outlets. Our consultants also had to deal with planning staff resources and warehouse organization support. The team cooperated closely with the architects to determine the required structural building modifications for future operations, e.g. openings or the installation of truck docking doors.
When the drawings of the central warehouse were available, we started to prepare tender documents for racking technology, the elevator system, various floor conveyors, and warehouse equipment. We conducted negotiations with suppliers and provided advice to the customer during the contract award procedure. Apart from warehouse logistics, our to-do list also included goods distribution. The important thing here was to create the prerequisites for optimal flows of goods with a view to the prompt and efficient supply of the stores and to find the right logistics service provider in the course of a tender procedure.
Help and advice on commissioning
During implementation, our consultants were not only providing assistance to the customer, but also to the building contractors or the IT department. Pragmatic solutions were soon found through direct exchanges if needed. After the warehouse team had been trained on the new processes, the new central warehouse with total logistics space of some 4,500 m2, including offices, a pallet warehouse and a three-story shelved racking system with some 10,000 rack spaces, was put into operation.
Challenging schedule – dynamic cooperation
Thomas Bale, Head of Consulting Lauterach mentions a “highly challenging schedule” that the parties had agreed on for this project: “The project started in spring and was meant to be completed by the end of the year.” Seasonal fluctuations and seasonal business as such have constituted additional challenges. According to Bale, it is due not least to the “dynamic cooperation” with Bründl that the logistics expert has managed to observe the deadline.